Während die formgebende Bearbeitung (NC-Fräsen, -Erodieren) von Spritzgieß- und Umformwerkzeugen in hohem Umfang automatisiert werden konnte, erfolgt die abschließende Oberflächenverbesserung immer noch weitestgehend durch manuelles Feinschleifen, Honen und Polieren. Die manuelle Feinbearbeitung bildet den letzten Prozessschritt der Werkzeugherstellung und ist somit entscheidend für die Produktqualität. Dabei hängen die Qualität und der Zeitaufwand ausschließlich vom individuellen Geschick des Handwerkers ab. Die daraus folgende schlechte Planbarkeit der Ressourcen, die immer knapper werdenden Fachkräfte und die schlechte Dokumentierbarkeit des Prozesses tragen ebenfalls zu den derzeit hohen Herstellungskosten der Bauteile bei.
Einen Ausweg bietet hier die zunehmende Automatisierung der Feinbearbeitung. Bisherige Lösungen können lediglich einfache bis leicht gekrümmte Oberflächen teilautomatisiert bearbeiten. Vor diesem Hintergrund besteht speziell aus Sicht der Werkzeug- und Formenbauer der Bedarf an neuen Werkzeug- bzw. Spindelsystemen für die Bearbeitung komplexer Geometrieelemente.
Auf Basis dieser Anforderung wurde ein Spindelsystem mit einer speziellen Fräs- Schleifspindel und automatisch auswechselbaren Bearbeitungsmodulen entwickelt, welche in Maschinen- bzw. Bearbeitungssystemen, wie Roboter oder 5- und 3-Achs-Fräsmaschinen, eingesetzt werden kann.
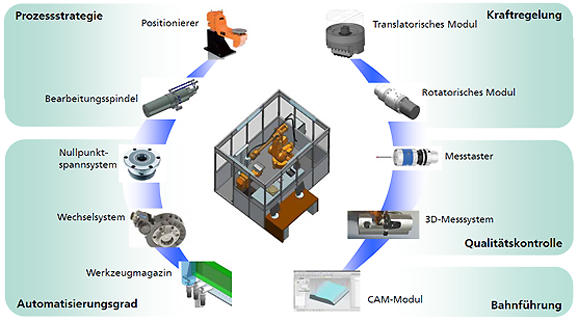
Bild 3: Robotersystem zur automatisierten Feinbearbeitung
Die Bearbeitungsmodule ermöglichen durch unterschiedliche Eingriffskinematiken und Kraftregelungssysteme einerseits die Feinbearbeitung komplexer Spritzgieß- und Umformwerkzeugoberflächen und andererseits die Kompensation des Werkzeugverschleißes und der Positionierungenauigkeiten der Maschinensysteme. Die Prozesskraft kann während der Bearbeitung kontinuierlich gesteuert oder geregelt und damit der jeweiligen lokalen Bearbeitungssituation angepasst werden.
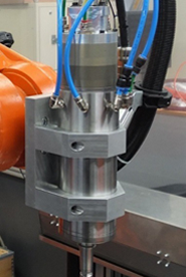
Bild 4: Spindel
mit rotatorisch axialem Modul
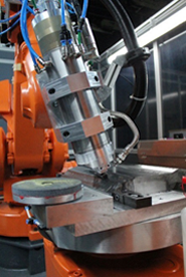
Bild 5: Spindel
mit translatorischem Modul
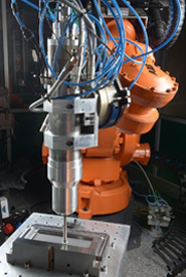
Bild 6: Spindel
mit rotatorisch radialem Modul
Vor allem im Formenbau besteht ein hoher Bedarf intelligente, der zu bearbeitenden Geometrie angepasste, Werkzeugsysteme bereit zu stellen um eine vollständige Bearbeitung aller Geometrieelemente eines Spritzgießwerkzeugs zu gewährleisten. Dies ist nur durch eine Kombination der verschiedenen neuartigen innovativen Werkzeugsysteme möglich.
Die einfache automatische Einwechsel- bzw. Austauschbarkeit und damit Kombinierbarkeit der Module gewährleistet eine erhebliche Steigerung der Verfahrensflexibilität und Maschinenaus-lastung. Je nach Bauteilgeometrie sind bei Bearbeitungsuntersuchungen Einsparungen der Bearbeitungszeit von über 50 % erzielt worden. Damit können die Herstellkosten in Größenordnungen von 15 bis 30 % und darüber hinaus gesenkt werden.
Wirkprinzip des Spindelsystems
Entgegen des herkömmlichen Bearbeitungsprinzips mit einem bahngesteuerter Abtrag, arbeitet das Spindelsystem mit einem Anpresskraft-Verweildauer erzeugten Abtrag. Die erforderlichen Anpresskräfte werden mittels Andruckelemente aufgebracht. Konstruktiv sind diese Elemente so gestaltet, das sie in einem definierten Anstellbereich eine konstante Anpresskraft ermöglichen. Infolge dessen wird das Werkzeug von der Bahn der Bearbeitungsmaschine bzw. des Roboters in Abtrags Richtung entkoppelt (die Bahn der Maschine kann innerhalb des Anstellbereichs der Module von der Oberflächengeometrie abweichen).
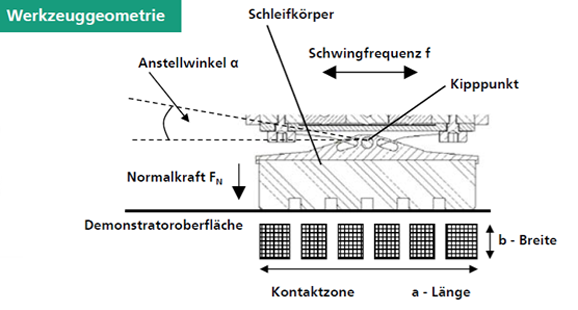
Bild 7: Werkzeuggeometrie des translatorischen Modul
Translatorisches Modul
Typische Spritzgieß- und Umformwerkzeuge bestehen aus einer Vielzahl von ebenen oder fast ebenen Geometrieelementen, die trotz unterschiedlichster Anforderungen an die Schleif- und Polierwerkzeuge, zur Vermeidung von Nebenzeiten, in einem Maschinensystem geschliffen und/ oder poliert werden sollen. Sofern die Zugänglichkeit der zu bearbeitenden Oberflächen gegeben ist, können plane oder gekrümmte, konkave sowie konvexe Flächen mittels des translatorischen Moduls mit axialer Kraftanstellung bearbeitet werden.
Bei den translatorischen Modulen ist ein vollflächiger Kontakt bei gleichzeitig geringerem Werkzeugverschleiß möglich. Die dadurch entstehenden markanten Vorteile sind neben einer nicht auftretenden Kantenverrundung , insbesondere das Entfernen der Oberflächenwelligkeit, die homogene Oberflächenqualität sowie die Erzeugung von Strichpolituren. Vor allem bei Blechumformwerkzeugen für die Automobilkarosserie sowie Spritzgießwerkzeugen sind diese Vorteile für lackierfähige Produkte von essentieller Bedeutung.
Je nach eingesetztem Grundmodul kann es unproblematisch in die jeweiligen Ausführungsvarianten Modul mit Wippe (Bild 8), Modul mit Segmenten (Bild 9) bzw. Modul mit Polierhebel (Bild10) umgerüstet werden. Der Arbeitshub ist standardmäßig in den Hublängen 2, 4 oder 6 mm, fest eingestellt. Optional ist auch eine variabel einstellbare Hublänge von 1 bis 14 mm wählbar.
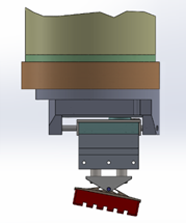
Bild 8: Modul mit Wippe
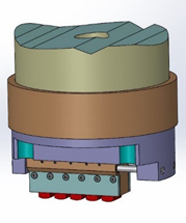
Bild 9: Modul mit Segmenten
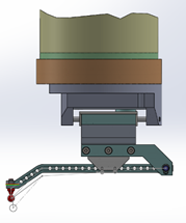
Bild 10: Modul mit Polierhebel
Um die Zugänglichkeit der Bearbeitungsmaschinen bzw. -systeme zu den zu bearbeitenden Flächen zu gewährleisten, sind die oben beschriebenen Module auch optional mit abgewinkelten Ausgleichssystem in den Winkeln 30°, 60° und 90° ausführbar (Bild 11).
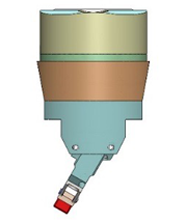
Bild 11: 30° abgewinkeltes Modul
Eine Sonderform des translatorischen Moduls ist das gegenläufige translatorische Modul mit seinen zwei Ausführungsformen des mittig (Bild12) und außermittig (Bild13) angeordneten Doppelschlittens, bei denen sich die Kräfte beider gleichgroßen, entgegengesetzt bewegenden Bearbeitungskräfte und Massen aufheben.
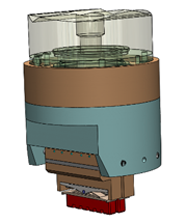
Bild 12: 30° Modul
mit 2 mittigen,gegenläufigen
Bearbeitungsschlitten
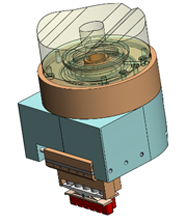
Bild 13: 30° Modul
mit 2 außermittigen, gegenläufigen
Bearbeitungsschlitten
Durch den Einsatz eines Schrupp- und eines Schlichtsteines wird die Produktivität des Moduls noch erhöht.
Rotatorisches Modul
Vor allem Spritzgießwerkzeuge bestehen neben einer Vielzahl von ebenen oder fast ebenen Geometrieelementen ebenso aus Vertiefungen und Löchern, die trotz unterschiedlichster Anforderungen an die Schleif- und Polierwerkzeuge in einem Maschinensystem geschliffen und/ oder poliert werden sollen. Sofern die Zugänglichkeit der zu bearbeitenden Oberflächen gegeben ist, können plane oder konkave sowie konvexe gekrümmte Grundflächen und Seitenwände mittels rotatorischen Modulen mit axialer und/oder radialer Kraftanstellung bearbeitet werden.
Im Gegensatz zu den translatorischen Modulen ist kein vollflächiger Kontakt sondern nur eine Punkt- oder Linienberührung des Werkzeuges auf der Bauteiloberfläche möglich. Bei Einsatz nachgiebiger Werkzeuge kann im begrenzten Umfang ein Flächenkontakt erzeugt werden.
Das Wirkprinzip der axialen Anpressung ist mit den Modulen mit radialer Anpressung kombinierbar.
- Rotatorisches Modul mit axialer Anpressung
Das Modul ist geeignet für die allgemeine Bearbeitung von gut zugänglichen konkav bzw. konvex gekrümmten Flächen sowie Grundflächen von Vertiefungen. Da die Anpressung in rein axialer Richtung bzw. mit leichter Anstellung des Werkzeuges bis max. 15° erfolgt, können mit diesem Modul auf 5-achs-Maschinen alle gut zugängliche Konturen bearbeitet werden. Der Aufbau ist relativ kompakt, da die Ansteuerung mittels Luft direkt über die Spindelwelle erfolgt.
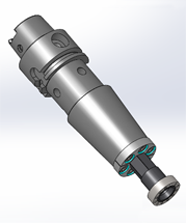
Bild 14: rotatorisches Modul
mit axialer Anpressung
- Rotatorisches Modul mit radialer Anpressung
Das Modul mit radialer Kraftanstellung soll in kraftgesteuerter Schleif- und Polierprozesse die Feinbearbeitung von Nuten und Wänden bei gleichzeitig reduziertem Programmieraufwand ermöglichen.
Das radial anstellbare Werkzeugsystem kann mit optimalen Eingriffsbedingungen bei maximalem Kontakt radial Prozesskräfte aufbringen. Das Modul ist so konstruiert, das die Anpresskraft Fr umlaufend (auf 360°) anliegt und innerhalb eines definierten Anstellweges konstant ist und sofort bei Auslenkung aus dem 0-Punkt anliegt.
- Rotatorisches Modul mit radialer Anpressung und schwenkender Auslenkung
Dieses Modul wird durch die radiale Pendelbewegung der rotierenden Bearbeitungsachse charakterisiert. Es ist vor allem für die Bearbeitung von Wandungen tiefer Geometrien wie Bohrungen und schmaler Durchbrüche gedacht. Durch die sehr lange Polierwelle (Bild 17) wird der Nachteil des Schwenkwinkels der Polierachse vernachlässigbar gering (ca.0,3° bis 0,45° je nach Polierwellenlänge).
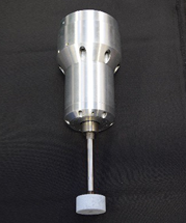
Bild 16: rotatorisches Modul
mit radialer Anpressung
und schwenkender Auslenkung
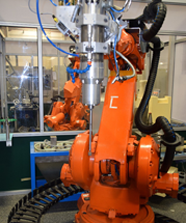
Bild 17: rotatorisches Modul
mit radialer Anpressung
und paralleler Auslenkung
- Rotatorisches Modul mit radialer Anpressung und paralleler Auslenkung
Das parallel auslenkende Modul ist für die Feinbearbeitung der Nutwände, die eine geringere Bearbeitungstiefe aufweisen vorgesehen. Dieses Modul ermöglicht eine parallele Auslenkung der Bearbeitungswelle zur Antriebsachse. Entgegen der Pendelauslenkung eignet sich die parallele Auslenkung der Werkzeugachse sehr gut für Bearbeitungsfälle mit linienförmiger Kontaktierung der Bearbeitungsfläche bei geringer Bearbeitungstiefe und höheren Bearbeitungskräften.
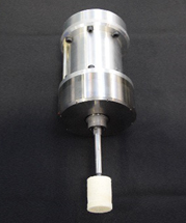
Bild 18: rotatorisches Modul
mit radialer Anpressung
und paralleler Auslenkung
Das Kugelkopfmodul ist für die Feinbearbeitung von konkaven Radien sowie freigeformten Oberflächen vorgesehen. Bei den (Bild 19 und 20) skizzierten 2-achs-Kugelkopfmodulen wird der Rotation des Modules durch die Arbeitsspindel eine zweite, elektrisch oder mechanisch erzeugte Rotation des Kugelkopfeswerkzeuges überlagert. Hierdurch kann ein entsprechendes Werkzeug ohne Anstellung, also senkrecht zur bearbeitenden Oberfläche geführt werden, ohne dass die Schnittgeschwindigkeit im Kontaktpunkt null beträgt.
Durch das Werkzeugsystem wird auch die Bearbeitung von Geometrien ohne zusätzliche Anstellung ermöglicht. Dieses ermöglicht erst die wirtschaftliche Bearbeitung spezieller Konturen auch auf 3-Achs-Maschinen und ermöglicht zudem eine signifikante Reduzierung des Programmieraufwands von ca.30% gegenüber der 5-Achsprogrammierung.
- 2-Achs-Kugelkopfmodul mit portalgelagerten Schleifkörper
Die Portallagerung der Werkzeugachse bedingt bei diesem Modul eine hohe Tragfähigkeit und Steifigkeit, wodurch Werkzeuge mit größeren Durchmessern eingesetzt werden können. Die rechtwinklige Anordnung der zwei Rotationsachsen erzeugt eine optimale Schnittbedingung im Kontaktpunkt.
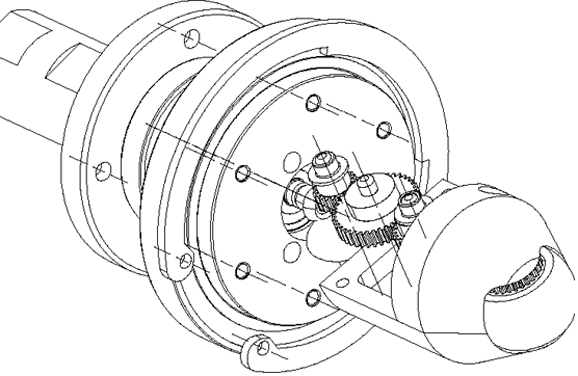
Bild 19: portalgelagertes 2-achs-Kugel-Kopfmodul
- 2-Achs-Kugelkopfmodul mit fliegendgelagerten Schleifkörper
Bei diesem 2-achs-Kugelkopfmodul kann das einseitig, fliegend gelagerte Werkzeug infolge des kinematischen Aufbaus einen Durchmesser kleiner 1 mm aufweisen. Aufgrund der winkligen Anstellung der Werkzeugachse wird die Störkontur verkleinert und der Werkzeugwechsel erleichtert.
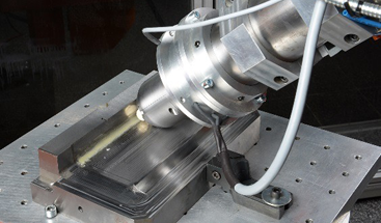
Bild 20: fliegend gelagertes 2-achs-Kugelkopfmodul
Anwendungsbeispiel
Fertigung eines Spritzgießwerkzeuges zur Herstellung des Gehäuseteiles mit hochglänzenden Flächen, das bisher sehr kosten- und zeitaufwändig von Hand feinbearbeitet wurde. Mit Spindelsystem und dessen Modulen, wird das Ziel, tagsüber zu fräsen und nachts automatisiert zu schleifen und zu polieren, nun umgesetzt. Damit werden die Produktivität und Verfügbarkeit gesteigert und die Herstellkosten gesenkt.
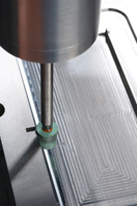
Flankenbearbeitung
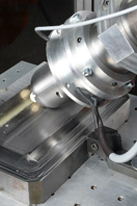
Radienbearbeitung
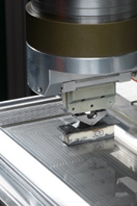
Flächenbearbeitung
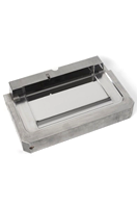
fertiges Teil